Safety
Ensuring employees are able to confidently perform their work in a safe work environment is critical to everything we do. Our employees are vital to our culture and performance in fulfilling the contract for ORISE, so we not only commit to a tradition of safety at work but strongly encourage our employees to carry this mindset beyond the workplace and into their homes and communities.
ORISE has held VPP Star Status since 2004.
Maintaining a commitment to safety means employees are trained in how to work safely and are obligated to watch out for each another, challenge, and report unsafe working conditions, follow all safety policies and procedures, and never take shortcuts at the expense of safety.
As a critical function of operations, ORISE’s Environment, Safety, & Health office manages the safety program with a focus on:
- Expertise from on-site staff who provide expert and timely services to reduce or eliminate occupational injuries/illnesses and hazardous exposures.
- Prevention activities and services that serve as the primary means of achieving our commitment to excellence in safety, health, and environmental programs.
- Continuous improvement to identify opportunities for improvement and ways to implement new technologies for enhancing program effectiveness.
- Leadership that demonstrates ORISE as a catalyst in implementing model environment, safety, and health programs for the DOE community.
ORAU, as managing contractor, is committed to performing work safely as it operates the Oak Ridge Institute for Science and Education. ORAU supports the U.S. Department of Energy policy of using management systems to integrate safety into work practices at all levels.
Integrated Safety Management
ORAU’s definition of “safety” encompasses environment, safety, and health, and also includes waste minimization and pollution prevention. All ORAU programs and departments actively pursue continuous improvement, and the addition of Integrated Safety Management (ISM) concepts further strengthens safety as a standard in ORISE’s culture. ORAU has accepted the ISM concept by contract under DOE Acquisition Regulations Clause 970.5204-2 and DOE Policy 450.4A, Integrated Safety Management Policy.
ORAU has also adopted DOE’s guiding principles and core functions of ISM on a corporate level and in all individual program/department/field office ISM plans. ORAU managers incorporate ISM into management and work practices at all levels to ensure that safety is an integral part of day-to-day activities.
ORAU endorses the ISM guiding principles as described by DOE and its Oak Ridge Site Office:
- Line management responsibility for safety
Line management is directly responsible for the protection of workers, the public, and the environment. - Clear roles and responsibilities
Clear and unambiguous lines of authority and responsibility for ensuring safety is established and maintained at all organizational levels and for subcontractors. - Competence commensurate with responsibilities
Personnel are required to have the experience, knowledge, skills, and capabilities necessary to discharge their responsibilities. - Balanced priorities
Managers must allocate resources to address safety, as well as programmatic and operational considerations. Protection of workers, the public, and the environment is a priority whenever activities are planned and performed. - Identification of safety standards and requirements
Before work is performed, the associated hazards must be evaluated, and an agreed-upon set of safety standards and requirements must be established to provide adequate assurance that workers, the public and the environment are protected from adverse consequences. - Hazard controls tailored to work being performed
Administrative and engineering controls are tailored to the work being performed to prevent adverse effects and to mitigate hazards. - Operations authorization
The conditions and requirements to be satisfied before operations are initiated are clearly established and agreed upon.
ORAU policies and procedures incorporate the five ISM core functions as defined by DOE:
- Define the scope of work
Missions are translated into work, expectations are set, tasks are identified and prioritized, and resources are allocated. - Analyze the hazards
Hazards associated with the work are identified, analyzed, and categorized. - Develop and implement hazard controls
Applicable standards, policies, procedures, and requirements are identified and agreed upon; controls to prevent/mitigate hazards are identified; and controls are implemented. - Perform work within controls
Readiness is confirmed and work is performed safely. - Provide feedback and continuous improvement
Information on the adequacy of controls is gathered, opportunities for improving the definition and planning of work are identified, and line and independent oversight is conducted.
Voluntary Protection Program
The U.S. Department of Energy’s Voluntary Protection Program (VPP) promotes public recognition of outstanding programs that demonstrate improved safety and health performance. VPP represents DOE’s high priority for operating in the safest way possible and brings several workplace advantages, including improved labor/management relations, reduced workplace injuries and illnesses, increased employee involvement, improved morale, and reduced absenteeism.
Our commitment to our Integrated Safety Management system has been recognized by DOE's VPP. ORISE originally obtained VPP Star Status in 2004 and has maintained the certification, earning multiple VPP Legacy of Stars awards.
ORISE emphasizes safety in every aspect of its operations, which are guided by the principles of an Integrated Safety Management system. ORISE’s commitment to incorporating VPP into its operations is reflected in five hallmark values:
The ORISE management team originally initiated the pursuit of VPP certification, and the team continues to promote safety with a goal to have zero accidents “by choice, not by chance.”
To encourage complete participation in the company’s safety program, employees are empowered to stop work at any point if they do not feel safe.
While most ORISE operations are conducted in typical office environments, there are several programs that involve workers handling radioactive or other toxic substances. Regardless of the type of work being performed, every work environment is thoroughly analyzed for all potential safety hazards.
Employee safety and facilities representatives (SFRs) meets quarterly to discuss safety issues and to receive continuing education on safety topics, which are then shared with fellow employees to keep them knowledgeable of ongoing safety topics.
As part of continuous improvement efforts, the ORISE Environment, Safety, & Health office sponsors mandatory, web-based training modules throughout the year that are focused on health and safety topics.
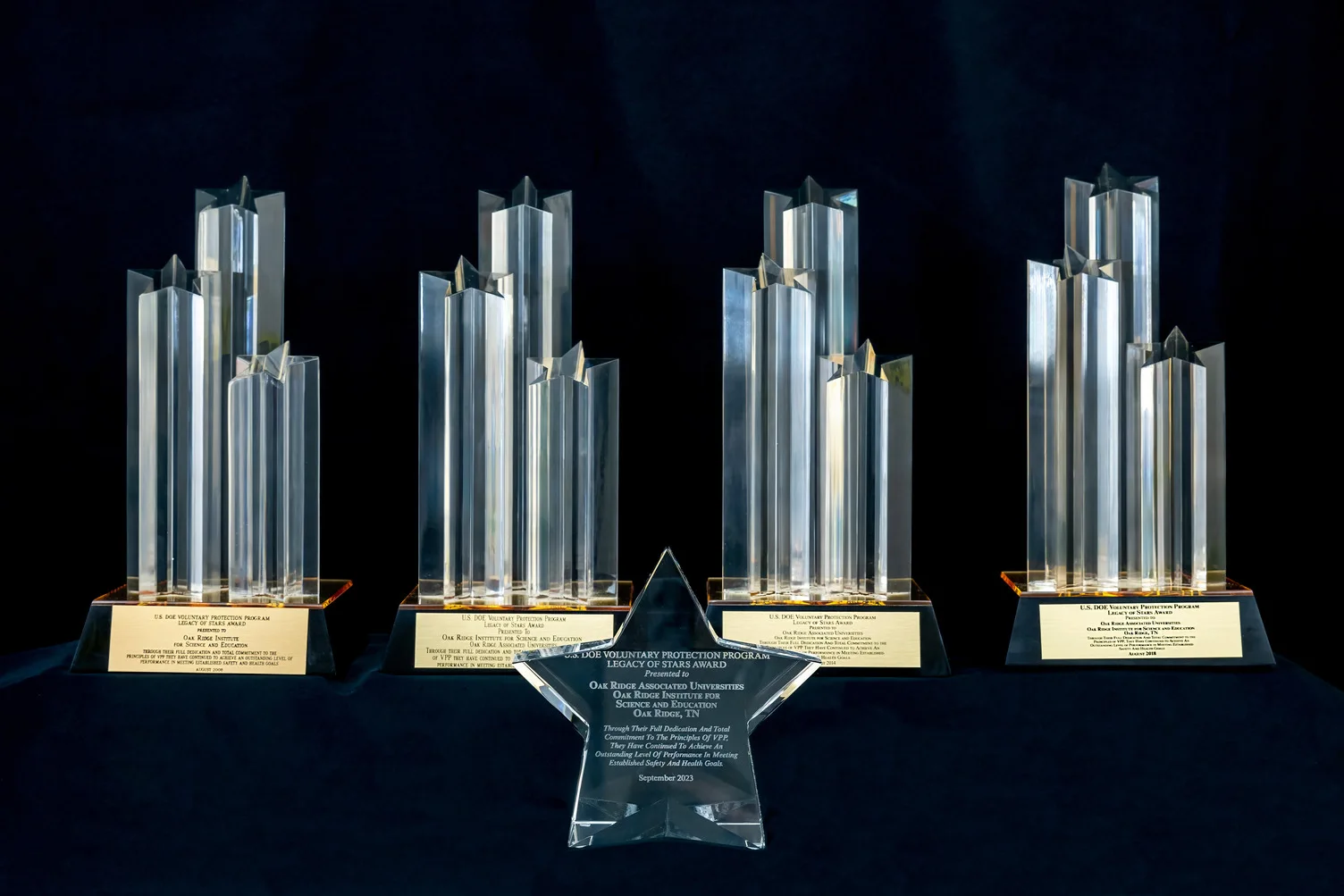
DOE Legacy of Stars awards